يمكن تقسيم إنتاج مقاطع النوافذ والبابات المصنوعة من الألومنيوم المزيج إلى أربع عمليات تقنية هي: تحضير الكواكب الصب، التشكيل عن طريق القص، المعالجة الحرارية والمعالجة السطحية. مع تزايد مستوى الحياة المستمر للناس، هناك طلب متزايد لون مظهر النوافذ والبابات. وفي تزامن مع تعقيد تقنيات معالجة الألومنيوم تدريجيا، نشأت بعض عمليات المعالجة السطحية المعقدة ببراعة. ومن بين عمليات المعالجة السطحية للفلومنيوم التي نرىها بشكل متكرر هي الكهربائية الالكتروفورسسية، الأكسدة الأنودية، رش الطلاء الفلوروكربوني وما إلى ذلك.
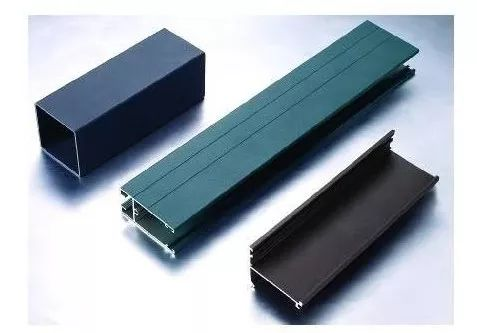
وهي عملية تتوزع فيها طلاء الكهربائية بين القطبين الموجب والسالب تحت تأثير الجهد الكهربائي. تتحرك أيونات الطلاء المشحونة نحو القطب السالب وتتفاعل مع القوة القاعدية السطحية للقطب السالب لتكوين مادة غير قابلة للذوبان وتترسب على سطح العملة. عملية الكهربائية الالكتروفورسسية للأشكال挤 من الألومنيوم المزيج تعني وضعه في حوض الكهربائية، ثم عندما يتم تمرير التيار المباشر، تتشكل على السطح طبقة راتنجات كثيفة. وتجعل الأشكال挤 من الألومنيوم المزيج المعدلة بالكهربائية الالكتروفورسسية ملامعة للغاية وتظهر لها تأثير مرآة، مما يزيد من مقاومتها للصدأ.
تقدم العملية:
تشير الأكسدة الأنودية للأشكال挤 من الألومنيوم المزيج إلى عملية تكوين طبقة أكسيد على制品 الألومنيوم (الأنود) في محلول إلكتروليتي محدد وبشروط تقنية معينة، وذلك بفعل التيار الم外加. ولكن طبقة الأكسيد الموجودة على السطح في حالة الأكسدة الأنودية تختلف عن طبقة الأكسيد العادية، فيمكن لطبقة الأكسدة الأنودية للألومنيوم التلوين عن طريق التلوين الكهربائي. من أجل التغلب على نقصات الصلابة والامتصاص في السطحيات للألومنيوم المزيج، وتوسيع نطاق تطبيقه، و연장 عمره، أصبحت تقنية المعالجة السطحية جزءًا لا غنى عنه في استخدام الألومنيوم المزيج، وإن تقنية الأكسدة الأنودية هي من أكثر التقنيات استخدامًا ونجاحًا حالياً.
تقدم العملية:
اختلاف بين الأكسدة الأنودية والكهربائية الالكتروفورسسية: في الأكسدة الأنودية، تحدث الأكسدة أولاً ثم التلوين، بينما في الكهربائية الالكتروفورسسية، يتم التلوين مباشرة.
يتم استخدام جهاز رش المسحوق الكهربائي لري spraying المسحوق على سطح العملة. تحت تأثير الإيجاد الكهربائي، يتم احتضان المسحوق بشكل منتظم على سطح العملة لتكوين طبقة مسحوقية. تمر هذه الطبقة مسحوقية في فرن حار لتهيئة وتصلبها، وتصبح طبقة نهاية ذات خصائص مختلفة. يتفوق أداء الرش على تقنية الرش بالطلاء كثيرًا في جوانب مثل الشدة الميكانيكية، التصاق، المقاومة للصدأ، والتحمل للشيخوخة.
تقدم العملية:
وهو نوع من أنواع الرش الكهربائي، وهو أيضًا طريقة الرش السائلة. يستخدم طلاء الفلوروكربون المرش بناءً على راتنجات البوليفيليден الفلوريد مع حرارة التزيين أو يتم مزجه مع مسحوق الألومنيوم المعدني كصبغة. هناك نوعان من الأساليب: المعلق والنصف معلق. في الأسلوب المعلق، يتم معالجة السطحيات والري spraying والتصلب للأشكال挤 من الألومنيوم المزيج أثناء تعلقها. تتميز طبقة الفلوروكربون الجيدة الجودة بلامعة معدنية، ولون واضح، وحس قوي من الثبات.
تقدم العملية:
اختلاف بين رش المسحوق الكهربائي ورش الفلوروكربون: يتم استخدام جهاز رش المسحوق (مكينة رش المسحوق الكهربائي) لري spraying المسحوق على سطح العملة في رش المسحوق الكهربائي. أما رش الفلوروكربون,则هو نوع من أنواع الرش الكهربائي، وهو أيضًا طريقة الرش السائلة، ويُعرف باسم رش الفلوروكربون، ويُعرف به في هونغ كونغ باسم كريما.
يشير الأشكال挤 ذات نقل تصميم خشب إلى عملية نقل تصميم خشب من ورقة نقل أو غشاء نقل إلى الأشكال挤 من الألومنيوم المزيج التي قد رُشت بالمسحوق أو معالجت بالكهربائية الالكتروفورسسية بناءً على مبدأ الارتقاء الحراري والتمتد الحراري. يتم ذلك من خلال تسخين وضغط. وتجعل هذه العملية الأشكال挤 خشبية ببنية واضحة وحس قوي من الثبات، وتجذب المزيد من الإحساس بالطبيعية للخشب. إنها مادة اقتصادية وصدية للبيئة مناسبة بدلاً من الخشب التقليدي.
تقدم العملية: